Practical Training is Key to Mastering Custom Metal Fabrication
While there are trade schools that promise a successful career in metal fabrication after a relatively short course, most successful metal fabricators attribute their success to practical training – not what they learned from a manual.
Custom metal fabrication demands precision and expertise that can only be gained through hands-on training. Practical learning empowers our employees to master complex techniques, operate state-of-the-art tools, and tackle problem solving and challenges with confidence. This direct experience accelerates welding skill development, and that results in workers being equipped to handle the unique demands of structural steel fabrication projects. Practical training is directly related to high-quality work and building a skilled, low-turnover workforce.
Understanding the Basics of Metal Fabrication
When you begin a career in metal fabrication, you will start with mastering the basic skills necessary for standard projects. There are many technical programs out there that offer to prepare you for a welding and metal fabrication career with a combination of coursework and interactive training. Most trade schools focus on giving you the knowledge and information that will allow you to gain hands-on experience and prepare you for the procedures you will need for an entry-level position.
You’ll be exposed to a wide range of welding procedures and practice welding in a variety of positions as well as practice many different techniques for cutting and preparing metal. While many aspiring metal fabricators will choose the trade school route, there is something special about a metal fabrication shop that offers on-the-job training to master these basic fabrication skills. Many metal fabrication experts will say that while their core knowledge is important, what really led them to success was extensive practical training with mentors.
Metal Fabrication Techniques
Metal fabrication encompasses many different skill sets, and before welders are ready to work on their own, they need to have experience in these commonly used techniques. As the basics are mastered, welders move toward more intricate projects. Before they can begin that training, they need to demonstrate not only proficiency, but skill in the overall fabrication process. While anyone can read a manual or watch a video explaining these techniques, until you have the equipment in your hands, you can’t hone these skills.
Bending and folding techniques manipulate sheet metal to create the right shapes and angles, and success requires practice with the proper techniques.
Forging and casting shape metal with heat through hammering with the right force or pouring molten metal into a mold to allow the metal to take on the proper shape.
These techniques have a long history and are mastered with practice and guidance from an experienced fabricator.
Machining uses drills and milling machines to remove unwanted and excess metal to create precise shapes. Machining allows fabricators to work with extreme accuracy, but the safety measures and skill with the equipment are paramount.
As you move through the basics, all of these techniques, alongside welding, need to be mastered with real, hands-on, practical experience before you are ready to tackle custom fabrication yourself.
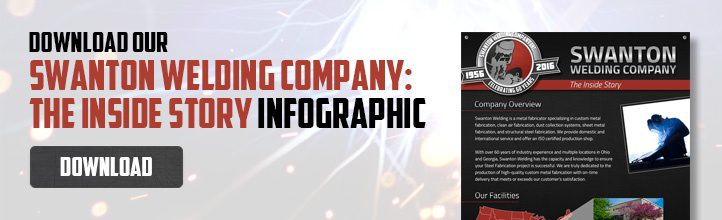
Custom Metal Fabrication
When you are working on a custom metal fabrication project, it is not enough to simply understand and be able to apply the basic fabrication skills, but you need to have mastered them to a degree where you can adhere to exact specifications, produce a product with precision and accuracy, and ensure that the final result is high-quality every time.
Using cutting-edge technology is often necessary for custom metal fabrication, and the margin for error is extremely low. Enough effective practice is needed for taking on a custom metal fabrication project, as the skills you will need should be nearly automatic so you can focus on meeting the customizations. It is extremely satisfying to take raw materials and create intricate structures and components that will be used in many different industries. The more experience you gain with master welders, the better equipped you will be to find your own success in custom metal fabrication.
Gaining Practical Experience
The best custom metal fabricators work in fabrication shops that value continued practice and learning, as well as a mentorship program that will help you move through the ranks and gain not only proficiency in fabrication techniques, but a standard of excellence. Having a mentor as you grow in your career in metal fabrication will allow you to gain the practical experience you need for custom metal fabrication projects.
If you’re looking for a solid career without the hassle and financial burden of going back to school, custom metal fabrication is a great choice. There’s a huge demand for skilled fabricators right now, and with the right shop and some hard work you can build a rewarding career.
The biggest decision you’ll make is where to kick things off. When you’re ready to get started, consider Swanton Welding Company. We’re all about valuing our team and providing a strong mentorship program. Plus, we invest in your growth, so you can keep learning and improving your skills. It’s not just another job; it’s a chance to start a fulfilling career where you can really make a difference. Contact us today!