Different Types of Abrasive (Sand) Blasting
Abrasive blasting, also called sandblasting, is used for finishing metal fabrication projects. Very small pieces or particles are propelled at a high rate of speed to clean the surface and prepare it for painting or other metal finishing techniques depending on the end use of the product. Sandblasting will remove mill scale, oil, and rust that can form on a freshly manufactured steel part, as well as removing other harmful surface contaminants that can damage the project. Manually cleaning the metal is a long and arduous process, and in contrast, sandblasting can be done quickly and easily. Sandblasting works well on many different projects, and the material selected for sandblasting will influence the final result.
Silica Sand or Silicon Dioxide
Silica sand is simply ordinary sand that can be found anywhere. Silica sand was once the primary method for sandblasting, as it can remove surface impurities and provide a clean smooth look without damage. However, other abrasives have been found to work just as well on different metal fabrication projects.
Soda
Soda sandblasting will not damage the outer layer of softer metals because it won’t react chemically and is not as abrasive as other materials. Delicate metal materials are often the best candidates for soda sandblasting. No damage or depression will be caused, but the grit will still give the cleansing and smoothing effect you can get from other harsher abrasives.
Steel Grit
Steel grit can be used for both blasting and scraping. Steel is abrasive enough to clean off corrosion and rust from hard metal surfaces and has a fast cutting effect that is effective in thick surface preparation prior to painting. Steel sandblasting is common in automotive, aeronautics, and heavy machineries. Steel grit leaves a smooth finish and is recyclable.
Glass Bead
Glass bead sandblasting is excellent for paint preparation and will provide a unique matte or satin finish to the metal surface. It will give a clean finish on a variety of metals, but softer metals, such as aluminum, are good candidates for glass beads. The beads are silica free and environmentally safe.
Bristle Blasting
Bristle blasting is only used on harsh surfaces to clean difficult corrosions or burrs. The steel bristles are arranged in a brush like fashion and rotated on the metal surface to remove impurities and therefore provide a smooth surface finish.
Benefits of Sandblasting
There are many benefits to sandblasting. Before your metal products are safe to use, you need to treat them to make sure there are no contaminants. Sandblasting provides a clean, smooth finish. The sand granules are small enough that their impact by compressed air cleans and smooths the surface, rather than denting it, all while removing rust and other undesirables. Sandblasting is eco-friendly, as it relies solely on physical abrasion as opposed to chemicals. There is no exposure to toxic chemicals, and the sand is natural and replenishable. Finally, sandblasting is efficient. Sandblasting completes the finishing process much faster than other metal finish treatments. The turnaround time is quick, which will shorten the overall project length.
Finishing your metal work is essential, and sandblasting is an excellent choice for many projects. When you partner with a metal fabricator, you can be sure that they will recommend the right sand blasting process for your particular fabrication project based on its make up and end use environment. Swanton Welding’s metal finishing department has the expertise, state of the art equipment, and deep understanding of the various metal finishing options to help you select the perfect finishing touch for your next metal fabrication project. Contact us today for a quote.
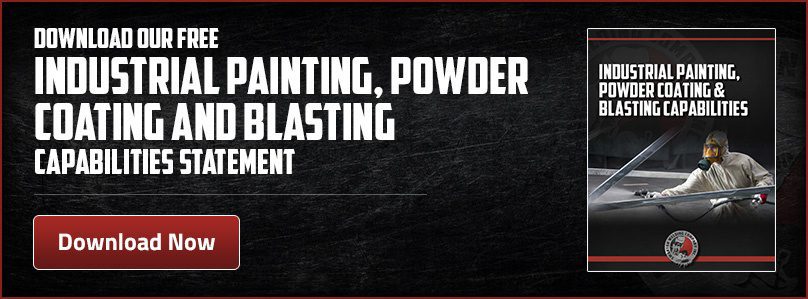