Finishing Your Products – Painting vs Powder Coating
When it comes to completing your welding/fabrication project, the choice of painting versus powder coating is often a tough one. In the end, both are worth your consideration, as both have unique pros and cons. Whether you are leaning towards a paint finish or powder coating, this information is bound to help you make the right decision.
To begin, here are the benefits of a paint finish for your welding/fabrication project:
Wet paint is the traditional route. The painting process is done through liquids and sprays. Both are viable options for an evenly coated finish, whether you want an ultra-thin finish or a thicker coating of up to 15-20micrometers. Painting also provides you with a wider range of colors to choose from and produces a thinner finish for your product. Wet paint is more economic when doing smaller jobs as well.
Painting is the ideal choice for finishing projects that are on a smaller scale. Not only will it be functional for your project, but it is also appealing. With the vast variety of color choices that painting offers you almost certainly won’t be disappointed by the finished look of your product.
Here are the benefits of a powder coating finish for your welding/fabrication project:
Economically, powder coating is ideal for larger projects because the average efficiency of such a coating is between 60-70 percent. This means that the overspray can be reclaimed, resulting in less wasted product. The base product used in powder coating is also significantly cheaper than other methods.
Powder coating is thicker than other finishes, contributing to the overall mechanical versatility of it. This translates into a more flexible, durable yield during and after application. A powder coating produces a harder finish than any other type, making it more resistant to chips or scratches.
Studies have shown that a powder coating can withstand cracking, flaking and bending up to 800% before failing. That is certainly more than can be said for most other types of finishes. As such It’s the ideal finish to administer to items that need to be transported because it protects the products from the wear and tear associated with vibration and movement during transport.
The environmental and safety benefits of a powder finish are also significant. Powder coating materials contain no solvents or volatile-organic-compounds. This means that there are no harsh chemicals released into the environment during application. Disposal is easier because of the lack of hazardous material in it. Due to this particular asset the waste can simply be disposed in your local landfill without issue.
As with any finish, you will want to use the proper personal protective gear to avoid irritation to skin or eyes. Fortunately, with minimal overspray and the absence of harmful solvents and volatile-organic-compounds(VOC), it won’t pose a health risk when applied correctly.
The value of using a powder coating for streamlining your product is also viable. This is the other advantage of using a powder coating, because after the product is removed from the oven, it takes less than 30 minutes for it to completely cure. This not only saves you time and money, but is ideal for mass production.
If you are still on the fence about making a choice between a paint or powder coating for your finish, here are the main differences between them: Painting provides you with a variety of colors to choose from and produces a much thinner finish than a powder coating can provide. Powder coating produces a thicker finish and has a limited amount of metallic colors to choose from, however it is more ideal for fiscally large projects and safer for the environment. Whichever product you choose, Swanton Welding can help.
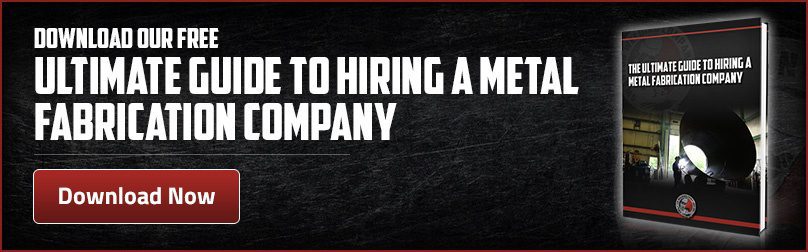