Building a Roller Coaster from Across the Country [Case Study]
At Swanton Welding Company we have a reputation for taking on large, challenging jobs. One of the more interesting ones we have taken on recently was manufacturing the parts used to build a roller coaster in California. While building something of this magnitude is difficult as is, we were posed with the unique challenge of having to do it from across the country. With focus on customer service and overall quality, our skilled employees were able to get the job done in only six weeks.
The Challenge
Building the roller coaster in such as short time frame was not the only challenge our welders were faced with. They also had to make sure that that the angles of the pipes would match up once they arrived in California. We had to utilize the expertise of our employees, as well as our state-of-the-art machinery as efficiently as possible to not only complete this project in a timely fashion but also make sure it shipped out and arrived on schedule.
How We Built and Tested it
Making sure that all parts of the roller coaster were not only sturdy but also resistant to the elements was another crucial part of the job. After constructing the roller coaster, we tested the welds for quality. In order to do this we used ultrasonic weld testing accompanied with a magnetic particle test to ensure the safety and quality of all the parts. The purpose for using the ultrasonic weld test was to find the location of any discontinuities that may have been in the welds. For this testing to be effective, it must be completed by an operator who is trained extensively in ultrasonic weld testing. A magnetic particle test was then used to detect the shape and size of discontinuities. This test is ideal for a job like this because it is not hindered by any traces of surface contaminants.
The Finishing Touch
Our GFS Downdraft Paint Booth was used upon completion of testing in order to blast the pipes and apply paint. This ensured that the pipes would be resistant to the elements and maintain their appearance over the course of their lifespan. This final touch provided the roller coaster with increased visual appeal as well as additional protection.
Materials and Labor Used
This roller coaster was created out of 200,000 pounds of complex pipe welded together by an ASME Section 9 Certified Welder. Certification for this title is prestigious, dictating that the welder must pass all required testing in order to be proficient with the contractor’s Welding Procedure Specifications. These specifications must also conform to any existing code requirements provided by the state.
While this was a unique and sometimes difficult job, our skilled welders at Swanton Welding Company proved that they were up for the challenge. From the construction of the initial welds, to making sure they fit perfectly together upon arrival, our team made sure that the job was done with quality and customization in mind. In the end, our goal is always to exceed our customer’s expectations and to produce only the highest quality products possible. If you need a welding or fabrication project done, no matter what the size, consider Swanton Welding.
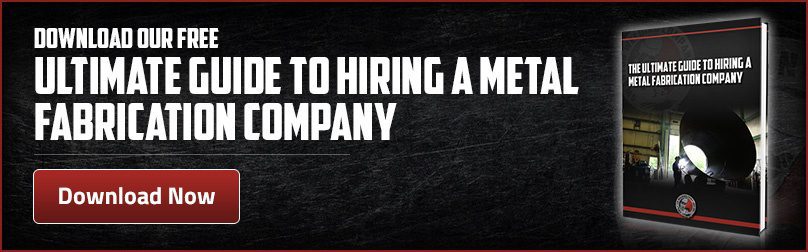