The Future of Welding: Trends and Innovations
Welding is an essential piece of the manufacturing and construction industry. Advancements in technology are providing improvements in quality, but are also making it essential for fabrication shops to stay up to date on the latest trends and innovations. As techniques, materials, and safety features advance, metal fabrication will be higher quality, longer lasting, and safer for workers. Finding a fabrication shop who is committed to continuous improvement and embraces the latest trends and innovations will positively impact the long-term success of your project.
Innovation in Materials
In recent years, metal fabrication shops have begun to use new and advanced materials. Alloys and composite materials are more durable, corrosion resistant, and lightweight than traditional metals, providing a significant advantage in manufacturing and construction. However, these new materials come with new welding techniques to achieve optimal results, and welders need education and training on how to work with these new materials. Aluminum-lithium alloys, carbon fiber, and fiberglass are becoming common in the automotive industry, as they are stronger than traditional aluminum alloys.
Traditional Welding Techniques
While there is still a place for traditional welding techniques such as gas welding, stick welding, MIG welding, and TIG welding, they do have limitations along with traditional advantages.
-
Gas Welding
Gas welding involves heating the two pieces of metal to be joined with a fuel gas, such as acetylene, and then applying a filler rod to create a fusion weld. This is a relatively slow process and is often not as strong as other techniques.
-
Stick Welding
Stick welding uses an electric current to create an arc. As the electrode melts, it creates a filler material to form the weld. Stick welding is usually used in structural steel projects.
-
MIG Welding
MIG welding is primarily used in the automotive industry. A wire electrode and inert gas are used to create the weld, offering higher speed and better penetration.
-
TIG Welding
TIG welding involves tungsten inert gas and a tungsten electrode to create an arc between the base metal and filler wire. TIG welding is high-quality and precise, usually used in aerospace, medical, and precision devices.
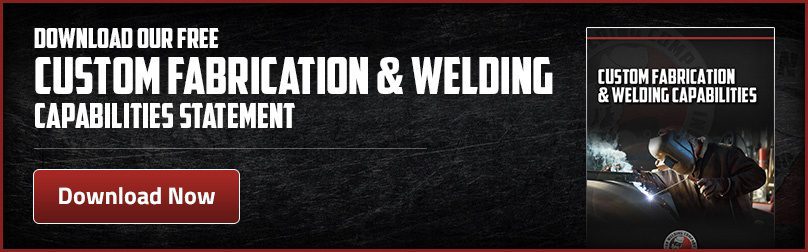
Advancements in Welding Techniques
While there is still a place for traditional welding techniques, advanced techniques are shaping the industry. Automated welding has many benefits, including efficiency, accuracy, and a reduction in human error. New automated welding techniques include:
-
Robotic Welding
Robotic welding uses automated robots, which can help remove workers from hazardous conditions and provide a degree of precision free from human error. Labor costs can be reduced, productivity can be increased, and welds are consistent, even on complex shapes.
-
Laser Welding
Laser welding is rising quickly in popularity. A focused high-energy laser beam is used to melt and join metal, making it an excellent option for applications in welding delicate and complex parts, such as aerospace and medical devices.
Advancements in Safety Features
The importance of safety in welding cannot be understated. Welding is a craft that comes with risks, but new advancements are focused on protecting the welders in addition to improving the quality of the welds. Recent developments in safety features like auto-darkening lenses in welding helmets, which can help in protecting the eyes of welders from the bright light produced during welding, and emergency stop buttons and over-current protection in machines that can help prevent accidents have all made a big difference in protecting welders from harm. Welding shops are investing more in personal protective equipment (PPE) including gloves, protective clothing to ensure the safety of their workers. Respirators and breathing protection devices have also been introduced to help welders avoid the harmful vapors that can be produced.
Artificial Intelligence in Welding
Artificial Intelligence (AI) has recently been used in the welding industry, which is helping to enhance efficiency, reduce waste, and improve quality. AI in welding includes making use of algorithms, sensors, and machine learning to optimize the process. AI helps to identify defects, adjust settings, and predict future needs. AI can help in optimizing welding parameters and perform automated inspection of welds. AI does currently have limitations due to the complexity of the technology and need for specialized training, but shops that are investing in implementation are seeing high quality results.
New Trends in Welding Quality Control
Through welding quality control practices, the welds are inspected to ensure that they meet the required specifications, internal flaws are detected, and weld failure is avoided. New trends in welding quality control have a focus on non-destructive testing methods, such as radiography, ultrasonics, and magnetic particle inspections. Testing welds has always been dangerous, as welds that fail can cause severe harm, and when destructive testing is used, the weld that was tested needs to be replaced with a new, untested weld, simply relying on similar methods to provide similar results. Non-destructive testing ensures that the weld that was tested is the weld that will be used. Ultrasonic testing, where high pitched waves are introduced via a transducer, is considered to be the best advance in welding quality control to date.

Welding is a dynamic industry and it is important that your fabrication partner will have professionals who are staying updated with the current trends. As innovations continue to evolve, there is a growing demand for highly skilled welders who are focused on constantly advancing their skills. When you are looking for a welding shop, look for one who has a focus on continuous improvement, with quality assurance processes already in place. To learn more about how we can help you with your next fabrication project, contact Swanton Welding for a quote today.