Trends and Technologies Shaping the Metal Fabrication Industry
In manufacturing, the metal fabrication industry stands as a symbol of innovation and adaptability, shaping the infrastructure of modern society. From the humble beginnings of manual crafting to today’s high-tech automated processes, the journey of metal fabrication has been remarkable. From architectural marvels to intricate machine components, metal fabrication plays a pivotal role in our lives. However, the industry is not stagnant; it evolves constantly, fueled by innovation and propelled by emerging trends and technologies.
Automation and Robotics
Integrating automation and robotics into traditional fabrication processes is one of the most significant transformations to date. Metal fabrication, historically labor-intensive, is witnessing a paradigm shift towards automation-driven efficiency. This innovation optimizes production lines, minimizing human error and significantly reducing production time.
Robotic arms with advanced sensors and programming can perform a myriad of tasks, from welding and cutting to bending and assembling with unparalleled precision and consistency. This enhances the quality of fabricated metal products, increases throughput, and lowers operational costs.
Automation in metal fabrication brings about a safer working environment for employees as well. Dangerous tasks that were once manually performed can now be executed by robots, mitigating the risk of workplace injuries.
Digitalization and IoT Integration
In the era of Industry 4.0, digitalization and the integration of Internet of Things (IoT) devices have revolutionized metal fabrication processes. Advanced software solutions coupled with IoT-enabled sensors offer real-time monitoring and optimization of production workflows.
These technologies enable predictive maintenance, where machines can anticipate potential breakdowns before they occur, minimizing downtime and maximizing productivity. Additionally, digitalization facilitates seamless communication between different stages of production, allowing for agile adjustments and optimization based on real-time data insights.
Furthermore, digital twin technology is gaining prominence in metal fabrication. Manufacturers can simulate various scenarios and fine-tune parameters before production by creating virtual replicas of physical processes and products. This reduces material waste for efficient resource utilization.
Additive Manufacturing (3D Printing)
The advent of additive manufacturing, or 3D printing, has disrupted traditional metal fabrication methods. Unlike subtractive processes like milling and turning, which involve cutting away material from a solid block, additive manufacturing builds objects layer by layer, offering unprecedented design freedom and complexity.
Metal 3D printing enables the fabrication of intricate geometries that were previously unattainable through conventional means. It opens doors to innovative product designs and lightweight, high-performance components. This is particularly evident in the aerospace, automotive, and medical industries.
3D printing reduces material waste by only depositing material where needed, leading to more sustainable manufacturing practices. However, challenges such as surface finish and post-processing requirements still need to be addressed for widespread adoption in specific applications.
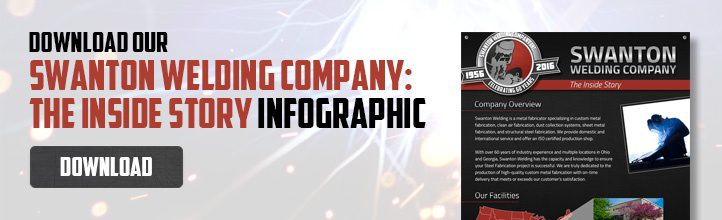
Advanced Materials and Alloys
The demand for lighter, stronger, and more durable materials has driven the development of advanced metal alloys in the fabrication industry. Innovations in metallurgy have led to the introduction of high-strength steels, aluminum alloys, titanium composites, and exotic metals with superior mechanical properties.
These advanced materials offer enhanced performance characteristics such as increased corrosion resistance, higher temperature tolerance, and improved fatigue life. They find applications in critical sectors including aerospace, defense, and renewable energy where reliability and performance are paramount.
The rise of sustainable manufacturing practices has spurred the development of eco-friendly materials with reduced environmental impact. Recyclable alloys and bio-based composites are gaining traction as manufacturers strive to minimize their carbon footprint and embrace circular economy principles.
Augmented Reality (AR) and Virtual Reality (VR)
Augmented reality (AR) and virtual reality (VR) technologies are revolutionizing how metal fabrication processes are planned, executed, and maintained. AR overlays digital information onto the physical world, providing real-time guidance and visualizations to operators during assembly, welding, and inspection tasks.
Conversely, VR immerses users in virtual environments, allowing immersive training simulations and design reviews. Engineers and fabricators can visualize and interact with 3D models of components, identify potential issues, and optimize designs before actual fabrication begins.
Moreover, AR and VR solutions facilitate remote collaboration, enabling experts to provide real-time guidance and support to field technicians or shop floor operators, regardless of geographical location. This enhances efficiency and reduces travel costs and downtime associated with onsite visits.
Emerging trends and technologies have profoundly transformed the metal fabrication industry. From automation and digitalization to additive manufacturing and advanced materials, these innovations have reshaped traditional processes, improved efficiency, and unlocked new possibilities in design and fabrication.
As metal fabrication shops embrace these trends and technologies, they position themselves to thrive in an increasingly competitive market. By staying agile, adaptive, and forward-thinking, manufacturers can harness the power of innovation to meet evolving customer demands, drive operational excellence, and shape the industry’s future.
Join the Future of Metal Fabrication with Swanton Welding
We are at the forefront of the metal fabrication revolution at Swanton Welding, embracing cutting-edge technologies and innovative processes to deliver unparalleled quality and efficiency. As highlighted in this article, our commitment to automation, digitalization, and advanced manufacturing techniques ensures that we stay ahead of the curve, offering our clients the best-in-class solutions for their metal fabrication needs.
Whether you require precision welding, custom metalwork, or large-scale fabrication projects, Swanton Welding is your trusted partner for excellence. Our skilled team leverages the latest trends and technologies to bring your visions to life with precision, speed, and reliability.
Don’t get left behind with traditional fabrication methods. Join us in shaping the future of metal fabrication. Contact Swanton Welding today to discuss your project requirements, get a quote, and experience the difference of working with an industry leader committed to customer satisfaction and quality.
