7 Benefits of Using Powder Coatings in Fabrication
Powder coating is an extremely popular means of painting your parts with a variety of colors and finishes available. It provides a number of benefits over traditional painting methods which can enhance the value and viability of the finish in a wide range of applications. From the cost of coating to the durability and environmental impact, powder is a very effective way to provide a high quality on your parts.
1. Very Efficient – Thanks to the electromagnetic charge used to hold the powder to the part, there is very little waste created in the process. In addition, your coating professional can spray as much or as little powder as needed in a single application. Rather than waiting for each coat to dry before applying the next, this is all done in a single step, and will still cure evenly. This saves time and money in operating costs.
2. Cost Friendly – In addition to the money saved by eliminating extra drying time and steps, powder coating is cost friendly in other ways as well. The raw materials used in the process are purchased specific to the size and specifications of the job at hand. The powder itself is less expensive than wet paint from the beginning, and can be stored in a way that takes up less real estate than paint cans.
3. Durability – In terms of the finish itself, powder coating is known for being far more durable than other paint options. During the curing process the powder melts and forms long chemical chains as it gels together. As a result, the finish is more flexible than traditional paint, and allows for a small amount of bending and flexing as your parts vibrate and move. It is also resistant to scratching, flaking, and corrosion.
4. Variety – While there are some common colors and finishes used in powder coating, one of the best assets of this method is the ability to completely customize your color and finish. The manufacturer will create a one of a kind powder blend that matches any color, with the option to add texture like wrinkles or glitter, and a huge range of finishes from high gloss all the way down to matte. Few other paint options can compete with this range and versatility.
5. Environmentally Safe – Since the powder used in powder coating it free of solvents and other chemicals, it is generally recognized as safe for use and for disposal. The process releases no known harmful chemicals into the atmosphere, and produces less overall waste throughout spraying. However, painters know not to inhale the powder and to wear protective gear to prevent skin contact.
6. Overall Quality – Both the application and curing process used in powder coating create a quality finish that is unlike any other paint on the market. Since the powder melts and flows together, it creates an even surface across the entire unit. In addition, it is not subject to unevenness, running or dripping, which are common among wet paints. As a result, it doesn’t require sanding or refinishing if a mistake is made.
7. Maintenance – Lastly, powder coating is extremely easy to maintain long term. No special cleaners or solvents are needed to keep it clean. Instead, it can be wiped down with regular, soapy water and rinsed off. Since the coating is so resistant to scratching and corrosion, you won’t have to worry about rust or other damage during cleaning. For most applications, wiping your parts clean a few times a year is enough to keep them healthy for many years to come.
It is easy to see how powder coating outperforms traditional paint options in a variety of areas. With the right equipment in place, it can cut down on finishing time, increase the quality of your finish, and open up a broader range of finishing options. It also allows you to store and dispose of materials in a more cost effective and environmentally responsible manner. Your customers will appreciate a finish that is wear and weather resistant, but also easy to maintain.
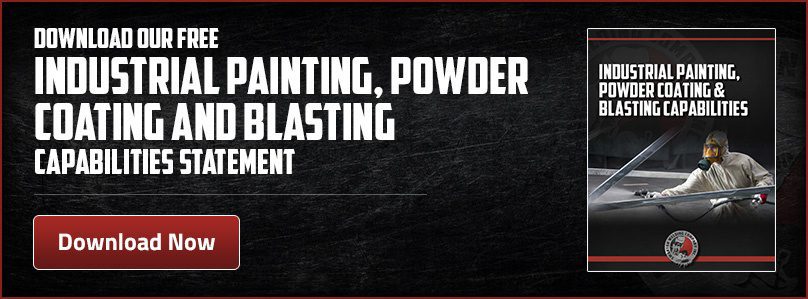