Supporting Structural Demands with Precision Welding
Swanton Welding is a fabrication shop that prides itself on supporting any structural demand with precision welding practices designed to meet the exact specifications of any unique project. Swanton understands that structural steel projects depend on exact standards to meet the demands of safety standards, longevity requirements, and durability needs. The success of any structural steel fabrication process relies on precision and quality. Swanton Welding is committed to meeting and exceeding these standards with our variety of welding techniques, the ability to adapt to each project, and high-quality requirements.
Use of Different Welding Methods
Different welding methods are used for various aspects of fabrication. One of the things that sets Swanton apart is our ability to design every project to meet the exact needs. Our team has mastered many different welding methods at Swanton Welding, including Gas Metal Arc Welding (MIG), Gas Tungsten Arc Welding (TIG), and Flux-Core Arc Welding.
- MIG Welding
Metal Inert Gas (MIG) Welding is the most commonly used welding technique, as it works well on many large fabrications with thick metal plates that need to be joined. MIG Welding uses a shielding gas along a wire electrode, which heats the metals needing to be joined.
- TIG Welding
TIG Welding is usually used on thick sections of stainless steel that use a tungsten electrode in a gas-shielded environment. This process is typically more time-consuming than MIG Welding and requires more technical skill from the welder. TIG Welding is used in aerospace and naval applications, where the weld needs to withstand extreme environments.
- Shielded Metal Arc Welding
This method is sometimes called stick welding and uses a coated welding rod that melts and creates a protective slag layer. The arc then melts the base metal and electrode, which forms the weld.
- Flux-Core Welding
Flux-core welding was developed as an alternative to stick welding and is usually used in construction projects. Because this method has so many variables, it can be used in various applications.
In addition to these methods, further precision welds have applications in fabrication projects, including gas welding, laser welding, electron beam welding, plasma arc welding, and more. At Swanton Welding, we not only have a team with the right experience in these various techniques, but we have also invested in the right equipment to support our team in safely honing their craft.
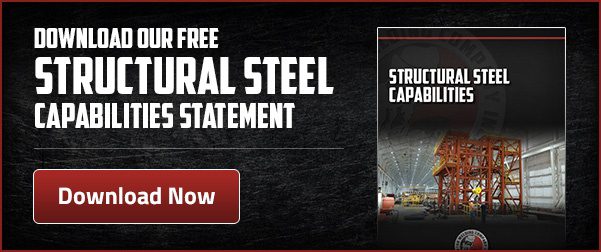
Choosing the Right Precision Welding for Every Project
Using the wrong welding method can lead to structural failures. With Swanton Welding’s team of certified and experienced welders, we have the right tools to choose the precision welding method needed for every aspect of your project. Our team has a collaborative approach, where we work together with the client to uphold the clear communication required to understand the exact specifications for the project, and our project managers take the lead to ensure that we choose the right precision welding processes that will avoid safety risks, delays, and costly mistakes. From intricate designs to crafting large-scale components, we know we have the right equipment and team for the job. Precision and accuracy are essential to success, and we will make sure every component is crafted to fit seamlessly into the overall project.
The Role of the Certified Welding Inspector
Swanton Welding has rigorous quality control procedures embedded into every part of the process. Every team member working on a fabrication project is held to strict standards and procedures to meet the precision, quality, and durability metrics. Swanton Welding has a quality control team, including a certified welding inspector, to conduct thorough inspections and use advanced testing methods to identify, address, and remedy any issues that may come up during the fabrication process. A Certified Welding Inspector is more than just a master welder; but has earned the credentials that demonstrate a thorough grasp of all welding processes and fabrication standards. To earn this certification, a candidate needs to pass several exams on fundamentals and codes, as well as a practical exam.
At the request of the customer, our Certified Welding Inspector (CWI) can verify that all welding processes, materials, methods, and procedures adhere to the proper welding codes and standards at Swanton Welding. The CWI does not simply come in at the end of the process to do a check, but is there throughout the fabrication, conducting visual inspections of the welds and performing all necessary tests and checks. Swanton’s CWI is responsible for documenting the entire inspection and remediation process and signing off on the overall quality. The CWI communicates with the whole team throughout the fabrication to make sure that the entire team is working together. Having a CWI involved throughout the project keeps the quality control aspect efficient, ensuring that every project is completed to the expected high standards and without delays.
What Sets Swanton Welding Apart
Swanton Welding has high standards for every project, every team member, and every process, and these standards that we hold ourselves to are reflected in the high-quality projects that keep every client satisfied. In an industry where precision and quality matter, we take the time to make sure that we manage your project efficiently, effectively, and accurately to get you the desired results.
When the success of your structural project hinges on precision, Swanton Welding is the partner you can trust. Our experienced team, certified inspectors, and advanced welding capabilities guarantee every weld is completed to the highest standards. Let us help you meet demanding specifications efficiently and accurately—contact Swanton Welding to get started today.
