Improved Fabrication Efficiency With Multitasking CNC Technology
When your project demands precision, speed, and reliability, you need a fabrication partner who’s already thinking a few steps ahead. At Swanton Welding, we don’t just keep up, we invest in the innovations that give your project a competitive edge. Our newest addition, the Mazak Quick Turn 250MY CNC Turning Center, is more than just a machine. Designed to streamline production, boost accuracy, and handle complex parts with ease, this advanced equipment allows us to deliver faster turnaround times, tighter tolerances, and greater flexibility. When you trust us with your fabrication needs, you deserve more than just capable. You deserve cutting edge.
Mazak Quick Turn 250MY KY Turning Center
Mazak’s machine tools, with their state-of-the-art technology and exceptional innovation, provide solutions to support CNC machining. The Mazak Quick Turn 250MY Turning Center takes CNC machining to the next level, and Swanton Welding is excited to have this available to better serve our clients. The Quick Turn 250MY Turning Center features:
- A built-in motor spindle with high-rigidity machine construction designed for exceptional performance.
- Milling, turning, and second spindle specifications specifically designed for production requirements.
- Minimized vibration with exceptional durability.
- Three types of turrets for different applications.
- A wide range of sizes and distance for tasks of all sizes.
- Contouring for high accuracy projects.
This model can perform a variety of tasks, from heavy duty machining to high-speed machining, with a variety of materials. The options to specify allow every project to be customized for your exact needs. The ability to ensure high precision while in a heavy machining process opens up many opportunities for our CNC team. As an American-made CNC turning center, we are confident that it will be able to deliver big results in a small footprint.
Multi-Tasking Capabilities
This particular model from Mazak will allow our fabrication team to excel at multitasking by integrating several different machining options into a single setup. Instead of needing to change machines for different processes like turning and milling, the new CNC lathe from Mazak has complete part machining capabilities that can take a variety of different raw materials and move them through the process. With these multi-tasking capabilities, lead times can be expedited, part cost can be reduced, and accuracy will increase. The single-machine setup reduces the potential for damage and operator error that can come from using multiple machines to move through the process. The low center of gravity and rigid bed design allows our team to handle both tough materials and more delicate materials that require more precision.
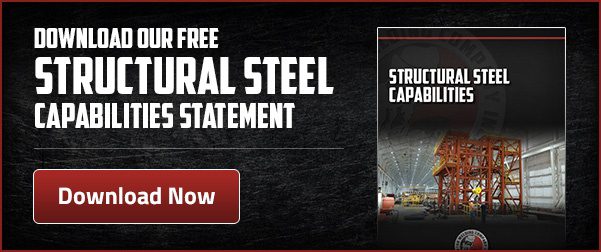
Complex Processes Handled With Ease
The new CNC lathe, with Y-axis movement and a powerful milling turret will allow our team to complete even the most complex parts that need machining, including components and steel enclosures. With fewer setups comes greater precision and better results. Our team is excited to serve many different industries with our improved capabilities.
Easy Programming
Machining is a skill that requires fabrication and programming skills. While our previous equipment can handle the fabrication requirements, programming has advanced significantly over the past thirty years, and the modern CNC interface and controls make programming this CNC lathe far more user-friendly than our previous equipment. When our operators can trust that the equipment is working well, they will not only have a more convenient experience using the machine, but will have better results.
Benefits of Upgrading
While Swanton Welding has always been committed to quality and innovation, our old CNC lathe has been serving us very well for nearly 30 years, and we know that it was time for an upgrade. The availability of the Mazak Quick Turn was the perfect opportunity to add it to our heavy fabrication facility. The features that we are most excited to work with are the bar feeder, which will feed the stock into the machine, making it effective when we are machining large quantities, and the live tooling allows our fabricators to use the same machine for mill operations, eliminating the need for a separate machine to finish the full project. This machine will increase our productivity, improve precision and flexibility, make the process easier for operators with a modern and upgraded interface, and provide the durability and power that we know our clients expect from our fabrication team.
At Swanton Welding, we’re committed to investing in the right equipment, our people, and our facilities—because we know that when we empower skilled operators with the tools they need, the results speak for themselves.
With a growing demand for turning work, now was the ideal time to upgrade. Our new machine, equipped with advanced live tooling and multitasking capabilities, is a strategic step forward. We’re excited to see how this investment enhances our precision, expands our capabilities, and ultimately delivers even greater value to our customers. To get a quote on your next project, contact us today.
