Understanding Your Spray Booth Filtration System
A spray booth is a sealed environment built for the specific purpose of applying spray paint, usually for motor vehicles. A spray booth is sealed to prevent dust and other particles from contaminating the air inside. These particles will affect the final paint finish. Clean air is blown into the spray booth using fans and then extracted using another set of fans. There are two types of airflow systems used in spray booths. A cross draft system moves air horizontally across the area from one end to the other. A down draft system moves air from the ceiling to the floor.
Filters are required to ensure that air entering the spray booth is free of contaminants and that air exiting it is free of hazardous chemicals.These filters play an important role in both ensuring quality paint work and that the workshop meets health and safety regulations. Filters are also used to ensure that air used in the spray hoses of free of contaminating particles.
Filters require regular maintenance in order to ensure that air both inside and outside of the spray booth is of the correct quality.
The Importance of Filter Maintenance
Through normal use filters become blocked with debris, reducing their efficiency. Filters that are no longer functioning properly, affect the airflow inside the spray booth. As a result dust and over spray are circulated inside the booth.
Poor quality air inside the spray booth will result in additional costs like buffing, color sanding, and spray booth cleaning. Most importantly extra time spent on corrective procedures results in less work being completed – making it difficult for you to meet your production targets.
When to Change Your Filters
There’s no exact way of telling at what time intervals filters should be changed. It depends mostly on the workload and type of booth. Paint booth manufacturers will recommend how long filters can be used before changing. Typically this will be about 60 hours.
Intake filters will be affected by the air quality of the local environment. If you’re in an area where there’s a lot of dust in the air, you’ll need to change the intake filters more regularly.
The type of booth you’re using will also affect how often filters need to be changed. Intake filters for a cross draft booth will need to be changed more often than down draft ceiling filters.
If you notice a drop in performance before filters are due to be replaced, it would be advisable to change them immediately.
If the spray booth is fitted with a manometer or velocity meter, this would be the preferred method of determining when to change filters.
Using a Manometer
- To calibrate your meter, turn the fans off and set the meter to zero.
- When the filters are new, run the fans with the booth doors closed. Observe the meter until the level stabilizes. Place a green mark at this point on the meter.
- Check the filter specifications for the recommended pressure differential. This is usually about one inch above the initial pressure level. So if the recommended differential is one inch, then place a red mark one inch higher than the green mark.
- When the level reaches the red mark, it’s time to change the filters.
Using a Velocity Meter
- When the filters are new and the fans are on, measure the velocity inside the booth. This should be at least 100 ft/min for most cross draft booths. This will be your green mark.
- Check what the recommended minimum velocity is for the booth you are using. This will be your red mark.
Changing the Filters
This is not a complicated process. Make sure that you have the recommended type of filters and that they are the correct size. There may be more than one filter for either intake or exhaust, so make sure you change them all.
Make sure that filters face the right direction:
- Exhaust filters need to have the open weave side facing the inside of the booth (inward).
- Cross draft intake filters should have the tacky side facing inward.
- Down draft intake filters use the mesh side facing inward.
- Pre-filters should have the tacky side facing inward.
Ensure that the booth fans are switched off before changing the filters.
Routine maintenance on your spray booth filtration system is not a complicated process and shouldn’t result in much downtime. The benefits of following the correct procedures as laid out above are self-evident.
Manufacturing a quality spray booth requires skill, experience and precision workmanship. To find out more on how to get the right spray booth for your requirements or anything you may need to know about spray booth repairs and maintenance, contact Swanton Welding Company for the best quality service and expertise.
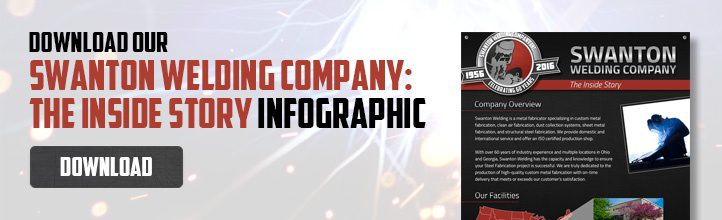