Project Spotlight: Fabricated Stainless Steel Catalytic Converter
When using stainless steel piping during the fabrication process, you typically find a seam running down the side of the pipe. As the steel is forged and twisted onto itself, the bonding point completing the circle creates this seem. While strong, the seam is the weakest point of any welded material.
To produce a seamless stainless steel cylinder, several varying options are often used, including injection molding. Clients looking for the strongest metal available should not only consider the quality of the metal but a lack of seams as well. Seamless tubes are a very important part of the construction of stainless steel catalytic converters.
Creation of a Fabricated Stainless Steel Catalytic Converter
Often found in vehicles, a catalytic converter is used to convert gas into exhaust, which reduces the pollutants emitted from the vehicle. Larger catalytic converters are used in manufacturing plants where exhaust gas is released into the atmosphere. Due to the sheer size of the building a high end catalytic converter is required. Swanton Weld recently took a job to produce a stainless steel catalytic converter for a plant on a tight time deadline. Efficiency was a must for the job, but it had to be done without sacrificing the quality of the converter. After all, an improperly made converter could lead to environmental damage.
Why Seamless?
When investigating the catalytic converter of an automobile you’ll likely find a seam somewhere in the tubing. Fuel emissions have improved over the last few decades, so the amount of emissions produced by vehicles has dropped. The tubing in the converter can handle all pollutants without allowing them to escape. However, in the production of a catalytic converter for a manufacturing facility it must be taken into account that buildings produce a substantially larger amount of toxic gases and pollutants in a shorter period of time than vehicles. This places pressure on tubing and welding points which are the weaker points of any welded item. This added pressure can result in leaks and cracks, causing pollutants to leak out into the atmosphere before being converted into exhaust.
There are environmental concerns behind the need to prevent these leaks, not to mention federal regulations. Seamless welding helps prevent these leaks as there are no longer any weak points. As such, reducing the total number of seams during the manufacturing of our client’s catalytic converter became a top priority for Swanton Welding.
Production of the Stainless Steel Catalytic Converter
The creation of a catalytic converter in a little more than a week was not a challenge for a company with Swanton Welding’s capabilities. However the creation of a seamless converter was more demanding. The company focused on reducing exposed welding points and making sure the converter was able to handle a set amount of pressure. The fabricated stainless steel catalytic converter took a total of 304 stainless steel sheets, seamless tubing, pipes, fittings, angle iron and bars in total.
To produce the seamless state of the converter, a considerable amount of rolling and forming went into the cylinders and cones. To bridge any gaps, the team used stainless steel flux cored welding wire, an especially strong bonding unit which increases durability while reducing the chance of separation or damage while in use. The catalytic converter needed to be as strong and durable as possible. Repairing the converter once it was installed would require the entire plant to shut down, costing the company potentially tens of thousands of dollars every day.
Completion
The completion of the fabricated stainless steel catalytic converter included the entire unit being wrapped in an insulation, followed by the insulation wrapped in an additional layer of sheet metal. Overall, the seamless tubing project went on without a hitch and the client was completely satisfied. It’s jobs like these that put Swanton Welding’s expertise and knowledge to the test, but in the end we were able to deliver a superior product. Contact Swanton Welding today for all of our seamless welding-related needs.
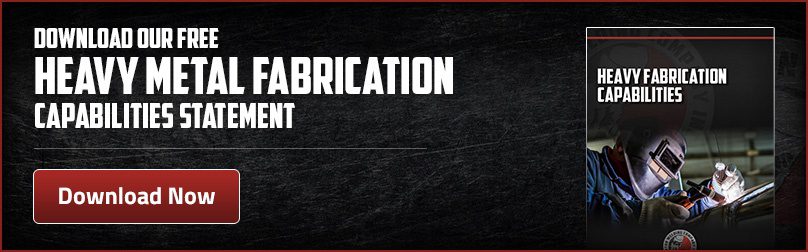