Water Tank Fabrication and the Parmigiani 4 Rolling Machine
Constructing welded steel water tanks is a highly specialized and exacting process that demands unwavering adherence to stringent standards set by the American National Standards Institute and the American Water Works Association. There can be no compromises when it comes to safety, no shortcuts when it comes to quality materials, and no room for subpar fabrication practices. Any deviation from these principles not only jeopardizes the integrity of the products but also endangers the lives of those who depend on them. To ensure that each project meets the highest standards of excellence, manufacturers must employ top-notch tools and highly skilled fabricators.
Steel stands out as an excellent choice for fabricating water tanks for various reasons:
- Strength and Durability: Steel is renowned for its exceptional strength and durability. It can withstand the significant pressure exerted by water, making it suitable for storing large volumes of water safely. This durability ensures the tank’s longevity, reducing the need for frequent replacements.
- Corrosion Resistance: Modern steel water tanks are typically constructed using corrosion-resistant materials, such as carbon steel with specialized coatings. These coatings protect the steel from corrosion caused by exposure to water, chemicals, and environmental factors. This corrosion resistance ensures the tank’s ability to maintain water quality.
- Hygienic Properties: Steel is a hygienic material that doesn’t promote the growth of bacteria, algae, or other contaminants within the tank. This is crucial for water tanks that store potable water, ensuring that the water remains clean and safe for consumption.
- Leak Resistance: Steel tanks are tightly sealed to prevent leaks and seepage. Welded seams and precise construction techniques minimize the risk of water leakage, preserving the water’s integrity and preventing waste.
- Customizability: Steel is highly customizable, allowing tanks to be designed to fit specific dimensions and capacity requirements. This versatility ensures that steel tanks can be tailored to suit various applications, from small residential water tanks to large industrial reservoirs.
- Environmentally Friendly: Steel is a sustainable material. It can be recycled and reused, reducing the environmental impact of tank fabrication and disposal. Additionally, steel tanks require less maintenance and since they are less prone to leaks, they reduce the potential for environmental contamination.
- Fire Resistance: Steel has excellent fire-resistant properties. In the event of a fire, a steel water tank can help supply firefighters with a reliable source of water for firefighting efforts.
- Ease of Inspection: Steel tanks are relatively easy to inspect for signs of wear and tear. Regular inspections can identify any issues early, allowing for timely maintenance or repairs to ensure the tank’s continued performance.
- Adaptability: Steel tanks can be easily modified or expanded to accommodate changing water storage needs. This adaptability is essential for industries and regions with fluctuating water demand.
- Cost-Effective: While the initial cost of a steel water tank may be higher than some alternatives, its long lifespan, low maintenance requirements, and durability make it a cost-effective choice in the long run. It minimizes the need for frequent replacements and repairs.
- Compliance with Regulations: Steel tanks can be designed and constructed to meet or exceed the stringent standards and regulations set by organizations like the American National Standards Institute (ANSI) and the American Water Works Association (AWWA). This compliance ensures that the stored water meets safety and quality standards.
Steel’s strength, durability, corrosion resistance, and other advantageous properties make it an ideal choice for fabricating water tanks, whether for residential, commercial, or industrial applications. It provides a reliable and long-lasting solution for storing and protecting water resources.
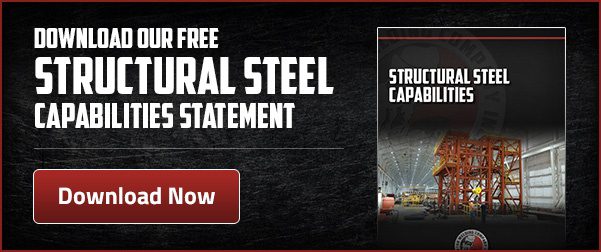
At Swanton Welding, we take great pride in our commitment to delivering exceptional metal storage solutions to clients nationwide. Central to our success is the utilization of the Parmigiani 4-Roll Plate Bending Machine, a marvel of precision engineering that sets new standards in sheet metal bending. This cutting-edge machine, crafted by one of the world’s premier manufacturers of metal bending equipment, exemplifies the fine Italian craftsmanship akin to renowned luxury car brands like Ferrari and Lamborghini.
So, what makes the Parmigiani 4-Roll Bending Machine the ideal choice for fabricating steel water storage tanks?
Complexity of Design and Fabrication
Designing and fabricating water tanks is inherently intricate. The process unfolds in multiple meticulous steps, ensuring that each tank adheres to the rigorous safety standards and regulations established by the American National Standards Institute and AWWA. The general process involves the following stages:
1. Detailed Design Specifications
Expert design engineers meticulously draw up specifications that will gain approval and surpass all safety guidelines. These specifications dictate the exclusive use of approved materials, such as carbon steel. Carbon steel then undergoes a highly specialized, multi-step coating process to enhance its strength and durability. Every aspect of the tank, from manhole covers to ventilation requirements, is meticulously constructed to exact standards.
2. Fabrication of Carbon Steel Sheet Metal Panels
Steel storage tanks are typically designed to be round, but steel sheets are inherently flat. Therefore, extreme pressure is applied to create precise bends that will eventually form the circular structure. Precision during the bending process is imperative. Each sheet must have the same inside bend radius as the others in its row to ensure thorough and precise welding at every joint. Here’s where the Parmigiani 4-Roll Bending Machine truly shines. Equipped with four fully hydraulic rolls capable of handling plate thicknesses up to 280 mm, this machine accelerates production while automatically forming metal bends with unparalleled precision.

3. Storage Tank Installation
Panel by panel, row by row, the tank takes shape on-site. This process involves meticulous foundation preparation, concrete work, and industrial welding before the tank is permanently installed. Special epoxy coatings are used to completely seal the tank bottom, ensuring its integrity. Every facet of construction is thoroughly scrutinized to ensure the tank can withstand internal and external pressures and endure the functional stresses that will come with use.
4. Field Testing for Quality Assurance
Rigorous testing throughout the process, especially at welded joints, is essential to detect any potential leaks or weaknesses promptly. Addressing vulnerable spots on-site ensures the tank’s safety and reliability.
5. Tank Completion and Certification
From top to bottom, every component of the finished storage tank must meet or exceed all regulatory standards to earn certification for use. Swanton Welding Company takes great pride in constructing superior storage tanks that inspire confidence in our clients.
Whether you require a steel storage tank for potable water, firewater, wastewater, mining, dry bulk agriculture, crude oil, or any other application, Swanton Welding possesses the expertise, specialized knowledge, and full capabilities to deliver projects of any scale. Contact us today for a quote.