Top Challenges in Welding Large Steel Structures and How We Overcome Them
Welding large steel structures can be a challenge. The integrity of a steel structure is crucial to the strength and success of the final product, and shortcuts cannot be taken. A high-quality steel fabrication partner will understand these challenges and work to anticipate any issues, allowing them to be avoided and mitigated.
The Challenges We Face in Welding Large Steel Structures
There are several challenges faced in welding large steel structures. Some of these include:
- Heat Management and Distortion
- Joint Access and Positioning
- Welding Quality and Integrity
- Safety Concerns and Environmental Factors
When contracting with a metal fabrication shop for a large steel structure, many of these issues can be avoided by finding a capable and experienced partner who holds certifications and employs best practices and quality assurance in welding techniques. You need a shop with experienced and expert welders who will be able to anticipate challenges and work to avoid them before they cause structural failures.
Overcoming Heat Management and Distortion
When welding, metal is heated, which causes the metal to expand and then contract as it cools. Distortion occurs as a result of this expansion and contraction. The affected areas can distort to a degree where it cannot be used in the final product. When temperature changes are not uniform throughout the metal, it can become stressed. In most cases, this distortion is because the metal has been clamped during the welding process. The metal is able to expand and contract only in the direction of least resistance, which is where it has not been clamped. This will result in the metal not being able to get back to the original shape. When the metal has not been clamped, it is free to expand in all directions, and when it cools down it will naturally contract back to the original shape.
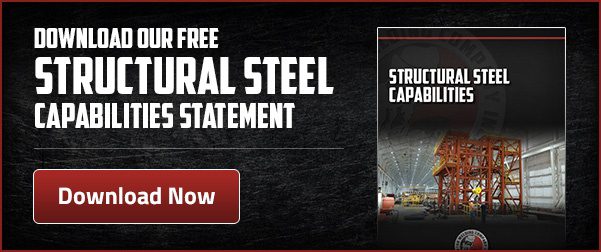
Eliminating distortion entirely is difficult, because you cannot fight the physics of expansion and contraction. The best way to combat distortion is to use welding techniques that control the distortion as much as possible. This is done by preparing the edges of the metal prior to welding. When the edges of the metal are beveled you will get good fusion on the weld while dealing with less distortion. Using tack welds spaced approximately twelve inches apart can help control distortion, as can quicker welding. Experienced welders will be able to weld quickly and still get good fusion, but this takes control. Intermittent welding, backstep welding, and pre-heating are also effective ways to reduce distortion from extreme heat. Using a jig, rather than a clamp, can also make a big difference.
Joint Access and Positioning
Welding joints are the connections between metal that are created during the welding process. Finding the right joints for every project is critical in determining the strength and quality of the finished product. Force, load, thickness, and resistance are some of the considerations when determining a welding joint, but sometimes finding access and a proper position for welding can make using the right type of joint difficult.
Understanding which joint technique to use is essential to the success of a welding project. The type of joint that will be accessible can depend on how the metal was prepared. When the weld metal does not extend through the joint thickness, there can be incomplete joint penetration, which will cause structural failure. An experienced welder will know how to look for the right fit and ensure that there is full penetration throughout the joint, allowing for integrity in the weld.
Welding Quality and Integrity
Quality controls and inspection protocols should be in place when doing any welding on a large steel structure. A welding procedure specification exists to standardize welding procedures and contains proven and tested methods to produce structures that are safe and compliant. Every metal fabrication shop needs to have documented inspection and quality control measures in place to ensure that all stainless steel welding is up to standard.
Safety Concerns and Environmental Factors
Welding is a dangerous process if you are not prepared. Welding safety involves wearing the appropriate protective clothing, checking and maintaining equipment, using proper gear, and following the shop safety protocols. All products need to be stored and treated correctly throughout the process, and proper ventilation is a must for fire and health safety precautions. Any metal fabrication shop should make safety paramount and continuously train and monitor staff for safety practices.
Welding does release pollutants into the air, but workers can use a variety of methods to reduce the environmental impact. Eco-friendly welding materials, the right welding process, reduced energy consumption, and proper waste management should all be in place to control the environmental impact.
Facing and Overcoming Challenges
A high-quality and experienced metal fabrication shop will understand the challenges of welding large steel structures and be ready to take them on with:
- Advanced welding techniques and technologies
- Precision planning
- Quality control and inspection protocols
- Safety measures and continuous improvement strategies

The integrity of a large steel structure is paramount to the success of the project, and that comes from the welding. Contracting with a shop that understands the importance of continuous improvement, certifications, the use of precision planning, advanced welding techniques, and quality control and inspection protocols can help avoid most challenges that will arise and ensure that your large steel structure will be successful. To learn more about our capabilities or to get a quote on your next project, contact Swanton Welding today.