What is Fatigue in Welded Steel?
Fatigue causes over 90 percent of failures in engineering components with welded steel parts. Fatigues on stationary equipment is a huge concern, however, it is crucial in mobile equipment, which experience unpredictable loads, making them susceptible to fatigue failures.
What is Fatigue?
Fatigue on welded steel occurs when you remove and reapply a load of insufficient magnitude repeatedly on a single application. When the load exceeds a certain threshold, it creates microscopic cracks on the steel, which gradually reach a critical size and propagate unexpectedly, causing structural failure. Several factors such as lack of fusion, shape, and lack of penetration affect the fatigue life of a structure. In welded steel, design flaws provide ideal sites for crack formation. In its entirety, fatigue failure happens fast, with a non-existent initiation phase.
What is Fatigue Life?
The term fatigue life in engineering refers to the number of stress cycles welded steel can sustain before a structural failure occurs. When dealing with steel, engineers always work with a theoretical value for stress magnitude, below which the steel will perform optimally regardless of the number of stress cycles.
Engineers testing the fatigue life of welded steel focus on deformations, internal defects, the welding technique, and stress concentration at the weld toe.
In identifying failure in welded steel structure and equipment, there are two common types of failures:
- Static Failure – Static failure begins with an obvious plastic deformation that you can easily detect and repair appropriately. Static failure rarely causes sudden and catastrophic accidents.
- Fatigue failure – Fatigue failure often begins with microscopic cracks that gradually increase in size, reducing the load-carrying effectiveness of an area. Failure to detect the cracks early often leads to sudden catastrophic structural and equipment failures.
Fatigue in Welded Steel
Over the past few decades, engineers have spent a lot of time researching fatigue failure in welded steel, while investing time and energy towards developing a system that allows them to predict service life and reduce the number of structural failures.
Due to the catastrophic nature of fatigue-related failures, there are different non-destructive techniques engineers use to inspect and test for fatigue tracks, for example, visual inspections and ultrasonic imaging among others. However, major achievements to help prevent fatigue-related catastrophes focus on welding techniques that address fatigue issues in the design and making of a weld.
Weld Improvement Techniques
Welding inherently reduces the fatigue life of steel parts and structures, presenting a continuous design challenge. There are different techniques designers and engineers use to increase the fatigue life and strength of welded steel, and subsequently, reduce fatigue-related structural failures. They include:
Weld Toe Grinding Techniques
A burr grinder uses a high-speed pneumatic grinder that moves at a speed of up to 40,000 rpm. Burr grinding removes surface defects and blends the weld metal with the base plate, which gives the weld a shape that reduces local stress concentration. The process focuses on removing defects and undercuts from the welded toe.
A disc grinder modifies the weld shape by removing slug inclusions and undercuts. In comparison to the burr grinder, it’s faster hence more cost-effective but also leaves grinding marks, which serve initiation sites for fatigue cracks. Disc grinding reduces the risk of fatigue incidents by 20 to 50 percent, which is relatively lower than using burr grinding.
Weld Toe Re-melting Techniques
The weld toe re-melting technique melts the weld region into a shallow depth, which substantially increases the fatigue strength of the weld joint. The re-melting process uses Plasma welding equipment or a Tungsten Inert Gas (TIG). The main shortcoming with this technique is that there is no inspection criterion to help you assess whether the process was satisfactory.
Peening Methods
Welding two materials together create tensile residual stress from the contraction of the weld once it cools, which weakens the steel’s fatigue strength. One way to improve the fatigue strength is to introduce compressive residual stress, which gives better results.
The penning techniques introduce compressive stress; it is a cold working process that impacts the surface with a tool or small metal balls creating plastic deforms. Ultimately, the penning process improves fatigue strength allowing higher steel strengths.
Stress Relief Methods
Unlike the peening method, stress relief methods work to reduce the tensile residual stress created by contraction. Stress relief techniques focus on refining the welding procedure and controlling temperatures that distort the weld.
Several industries, manufacturers, and tools use welded steel for their parts. Understanding the internal factors that contribute to the failure of the equipment is crucial to the design process. Designers working with welded steel can create machinery that addresses fatigue issues from the start. If you have a fabrication or welding need, contact Swanton Welding. Our innovative technology and expert welders will provide you with a great product every time.
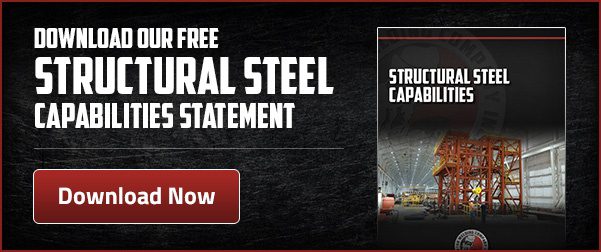