Advantages of Roll Forming Custom Metal Parts
Roll forming is gaining in popularity due to its flexible and cost-effective process of custom shaping metal. Roll forming is also known as “cold roll forming”, because the metal is shaped in a hardened state. Roll forming has many benefits over other approaches for many applications.
Roll Forming is Efficient and Quick
Because roll forming is done with long strips of metal in coils, the process is fast, allowing for high volume production with a great deal of efficiency. When compared with press braking or stamping, roll forming is far more efficient. Punching, notching, or other additional processes can be incorporated into the roll forming production line, which will further increase efficiency and produce custom metal parts that are ready for distribution right off the line, rather than requiring separate processes for each need.
Metal Roll Forming is Cost Effective
Because roll forming is a no-heat system, it requires less energy, reducing costs over traditional forming systems that do require heat. Because roll forming does not create the same wear and tear as stamping or other processes, it can eliminate the need for machining. Lower labor demands will further reduce the cost of this custom metal fabrication process.
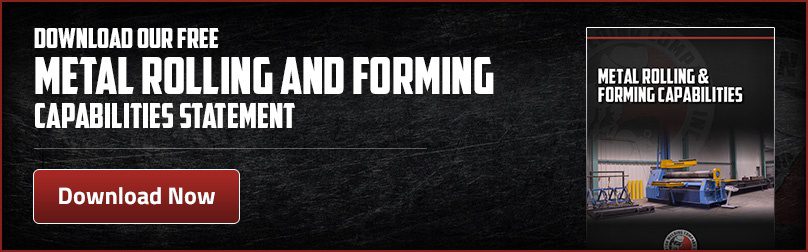
Custom Length and Less Waste
Press braking may limit the length to the size of the machine, but roll forming means that parts can be made at any length required. Identical parts cut from long strips means almost no wasted scrap, making this process a very cost-effective choice. Production time can be reduced significantly with roll forming as well.
Metal Roll Forming Can Create Uniform, Consistent Parts
Some metal fabrication processes are limited to which metals can be used, but almost any metal, ferrous or non-ferrous, can be roll-formed. Roll forming is designed to meet very tight tolerances and products will be uniform and consistent across the runs.
Cross Section Profiles are Easily Created
Complex cross-section profiles can be easily created with roll forming. Round, closed, and C-shaped profiles can be easily handled with roll forming. When quantities are more substantial, roll forming is a much better choice than metal stamping. The stable process of roll forming is capable of creating cross-section profiles easily, with less tool maintenance required.
The Best Equipment Makes the Best Product
To meet your exact specifications in custom metal parts fabrication, a metal fabrication shop needs the best resources. Top-of-the-line equipment, combined with experienced fabricators can ensure a successful run.
Our metal rolling and forming services recently improved dramatically with the acquisition of a Davi MC4P11, the industry-standard when it comes to metal rolling and forming. Italian-made from the same region that produces Lamborghinis, Maseratis, Ducatis, and Ferrari. Quite frankly, Davi-produced equipment performs up to those same “Made in Italy” standards. Davi ensures every MC4P11 they produce meets their rigorous standards by only sourcing parts from suppliers that are ISO 9001-certified.

While not every product will need roll forming, cold roll forming is an excellent choice for metal fabrication in many different industries. Having the best equipment will only add to the benefits of roll forming. With top-of-the-line equipment, an excellent fabrication team, and the right methods, your custom metal fabrication project can be completed efficiently and effectively.
By combining the best metal fabricating professionals in the midwest with the world’s best technology, there’s no one that can match the overall quality and customer service that Swanton Welding can offer. Contact our team to learn more about the impact Swanton Welding can make in your next custom metal project.