Laser Cutting: The Right Choice for Your Next Metal Fabrication
Selecting the appropriate cutting method in steel fabrication is essential for precision, material preservation, efficiency, cost optimization, flexibility, and ensuring high-quality outcomes. By investing time and expertise in evaluating and choosing the right cutting technique, you’ll set your project up for success in the field.
Precision and Accuracy: The accuracy of the cutting method directly impacts the quality and fit of the fabricated components. Steel fabrication often involves intricate designs and precise measurements. Using the wrong cutting method can result in inaccuracies, compromised dimensions, and ill-fitting parts, leading to rework, delays, and additional costs.
Material Preservation: Each cutting method has an effect on the material being cut. The right cutting method ensures minimal distortion, warping, or damage to the steel, preserving the integrity of the material. By choosing the appropriate cutting technique, you can reduce material waste, optimize material usage, and achieve higher yields, thereby saving costs.
Efficiency and Time Savings: Steel fabrication projects often have strict timelines, and delays can have cascading effects on the entire production process. The right cutting method, such as laser cutting, offers high-speed and precise cutting, resulting in faster production times. By minimizing the time required for cutting and processing, it’s easier to adhere to project schedules and meet deadlines.
Cost Optimization: Opting for the correct cutting method can lead to significant cost savings. Efficient cutting methods minimize material waste, reducing the need for additional raw materials. Moreover, faster production times achieved through the right cutting method translate into lower labor costs and improved operational efficiency. Choosing the most suitable cutting method is a way to optimize costs without compromising on quality.
Flexibility and Adaptability: Different cutting methods have varying capabilities, thickness limitations, and compatibility with different metals. The right cutting method offers versatility and adaptability, enabling fabricators to work with a wide range of sheet metal thicknesses, materials, and complex designs. This flexibility allows for seamless integration into diverse fabrication projects, ensuring the desired outcomes can be achieved regardless of project specifications.
Quality and Customer Satisfaction: The quality of the final product depends heavily on the accuracy and precision of the cutting method. By choosing the right cutting technique, you can deliver high-quality components that meet or exceed expectations. Consistent and precise cuts contribute to the overall aesthetics, functionality, and durability of the fabricated steel products.
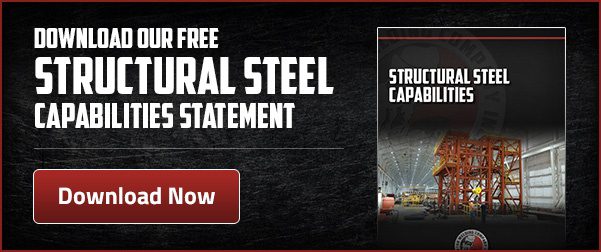
Laser Metal Cutting
Laser metal cutters are renowned for their precision, producing smooth and clean cuts that often require minimal post-cutting processing. This characteristic proves invaluable when meeting tight deadlines and helps reduce manufacturing costs.
Efficient and versatile, laser metal cutters can be programmed to transition seamlessly from one metal to another, facilitating the cutting of various thicknesses. This flexibility minimizes the need for extensive tooling changes, resulting in time savings during the fabrication process.
Unmatched Precision
The tight focus of the laser beam ensures precision cutting with minimal heat-affected zones. The concentrated heat application enables fine, accurate cuts, enhancing the overall quality of the fabricated components.
Laser metal cutting is highly efficient, reducing man-hours and minimizing material waste. By streamlining the fabrication process, laser cutting helps improve overall efficiency and lowers costs, making it an attractive choice for projects with budget and timeline constraints.
Choosing the Right Cutting Method
When working within budgetary and timeline constraints, selecting the most efficient cutting method is crucial. Avoiding unnecessary mistakes, material wastage, and complex programming helps streamline production and minimize costs. It is essential to rely on experienced experts who possess the foresight and knowledge to determine the cutting method that best aligns with your design specifications.
Laser metal cutting has become a game-changer in the field of steel fabrication. Its remarkable precision, versatility, and cost-saving advantages make it an ideal choice for numerous applications. By harnessing the power of laser technology, fabricators can achieve smooth and clean cuts with minimal post-cutting processing, resulting in improved efficiency, reduced waste, and significant cost savings. When it comes to sheet metal cutting, laser cutters have proven their worth by delivering high-quality results within tight timelines and budgets. As technology continues to advance, laser metal cutting is poised to play an even more prominent role in the future of steel fabrication, revolutionizing the industry and meeting the evolving demands of modern projects.
At Swanton Welding Company, our skilled machinists and fabricators are well-versed in utilizing various precision cutting methods to deliver high-quality results. With our extensive industry experience, we can handle your next custom metal fabrication project with ease. Contact us today for a quote.
